К вопросу о долговечности ходовых колёс мостовых кранов
Наши выводы, технические решения и результаты:
1. ООО «Эл-Кран» с первого дня образования собственного производства закупает на склад и изготавливает колёса крановые только из высококачественного сырья. Мы принципиально не используем в производстве литьё ни для изготовления собственной продукции, ни при работе по кооперации с использованием давальческого материала. Все материалы закупаются только у известных и проверенных поставщиков и имеют сертификат качества. Впоследствии, сертификаты прилагаются к паспортам на готовые изделия и передаются заказчику вместе с продукцией;
2. Особое внимание мы уделяем упрочнению рабочей поверхности колеса кранового. На вооружении ООО «Эл-Кран» имеется инновационный компьютеризированный участок термической обработки, состоящий из современной программируемой электрической шахтной печи и специализированного комплекса для сорбитизации колёс крановых.
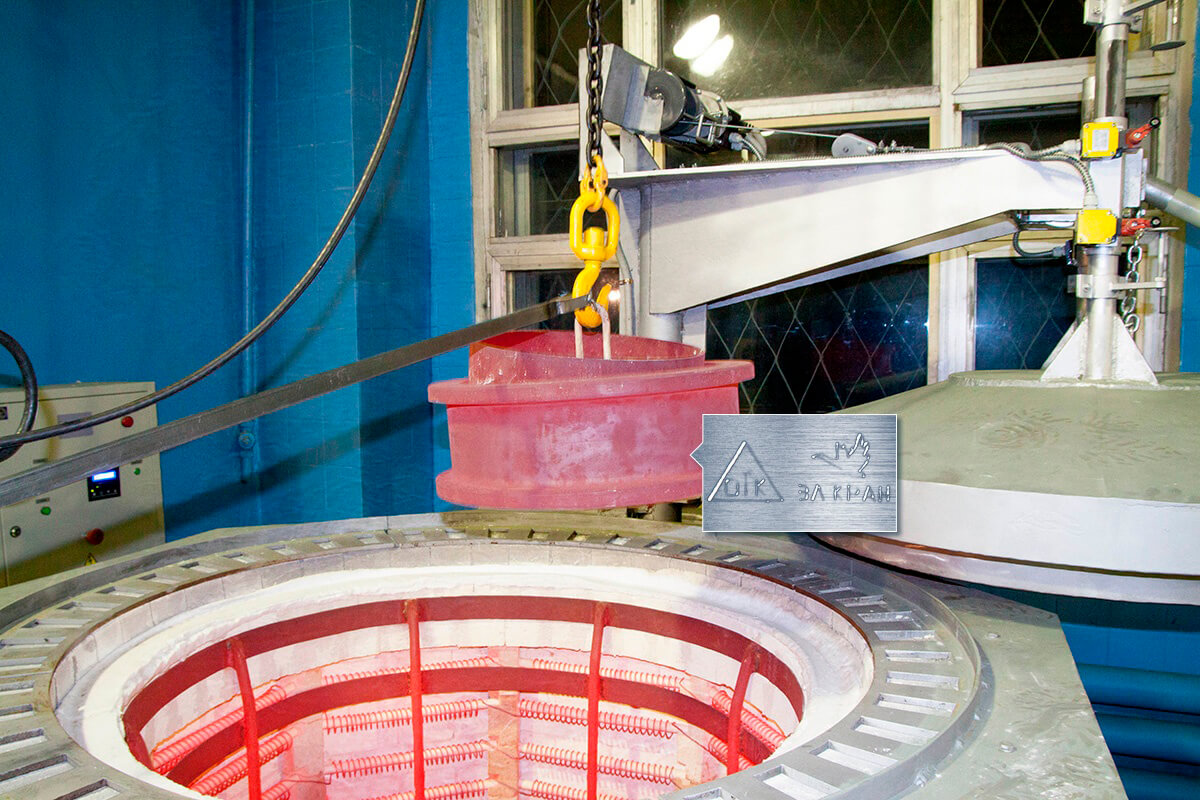
Фото 1. Термическая обработка крановых колес
Это позволяет нам тщательно подбирать и жёстко контролировать различные режимы закалки рабочих поверхностей колёс (скорость нагрева с выдерживаемой точностью +/-1˚C, зонирование закаливаемых участков, интенсивность охлаждения, состав, давление, температуру охлаждающего агента). В результате мы получаем заранее требуемый нормируемый показатель твёрдости рабочих поверхностей колеса кранового в более узком диапазоне, чем регламентирует ГОСТ 28648-90 (п. 2.4. Твёрдость поверхности катания и реборд,…, должна быть от 320 до 390 НВ) - требуемый диапазон - 70 единиц (НВ). Колёса производства ООО «Эл-Кран» имеют нормируемый показатель в более точном диапазоне – 25…30 единиц (НВ). Кроме того, мы имеем гарантированные и проверенные показатели колёс по глубине закаленного слоя и плавности перехода закаленного слоя к незакаленному.
Кроме того, принимая во внимание все нюансы вышеприведённых изысканий по вопросу износа и долговечности колёс крановых, а именно то, что реборды колёс подчас подвергаются несколько большим нагрузкам, мы научились дифференцировано улучшать рабочую поверхность колеса кранового, путём зонирования закаливаемых участков. Таким образом, реборды на наших колёсах получают твёрдость на 20…25 единиц(НВ) выше, чем поверхность качения. В том числе, зонирование при термообработке позволяет применить эффект дополнительного отпуска-нормализации нерабочих участков колеса (ступица, зеркальный диск), обеспечивает высокую надёжность конструкции колеса в целом, придаёт необходимую структурную упругость, улучшает ударную вязкость. Исключает риски, присущие колёсам, подвергшимся объёмной закалке: высокая отпускная хрупкость, большие разнонаправленные напряжения в структуре кристаллической решётки, как следствие склонность к растрескиванию и внезапному разрушению. Так же, такое избирательное отношение к термообработке различных участков колеса позволяет выполнять дополнительную механическую обработку с высокой точностью: выполнение шпоночного паза, сверловка монтажных отверстий и пр.;
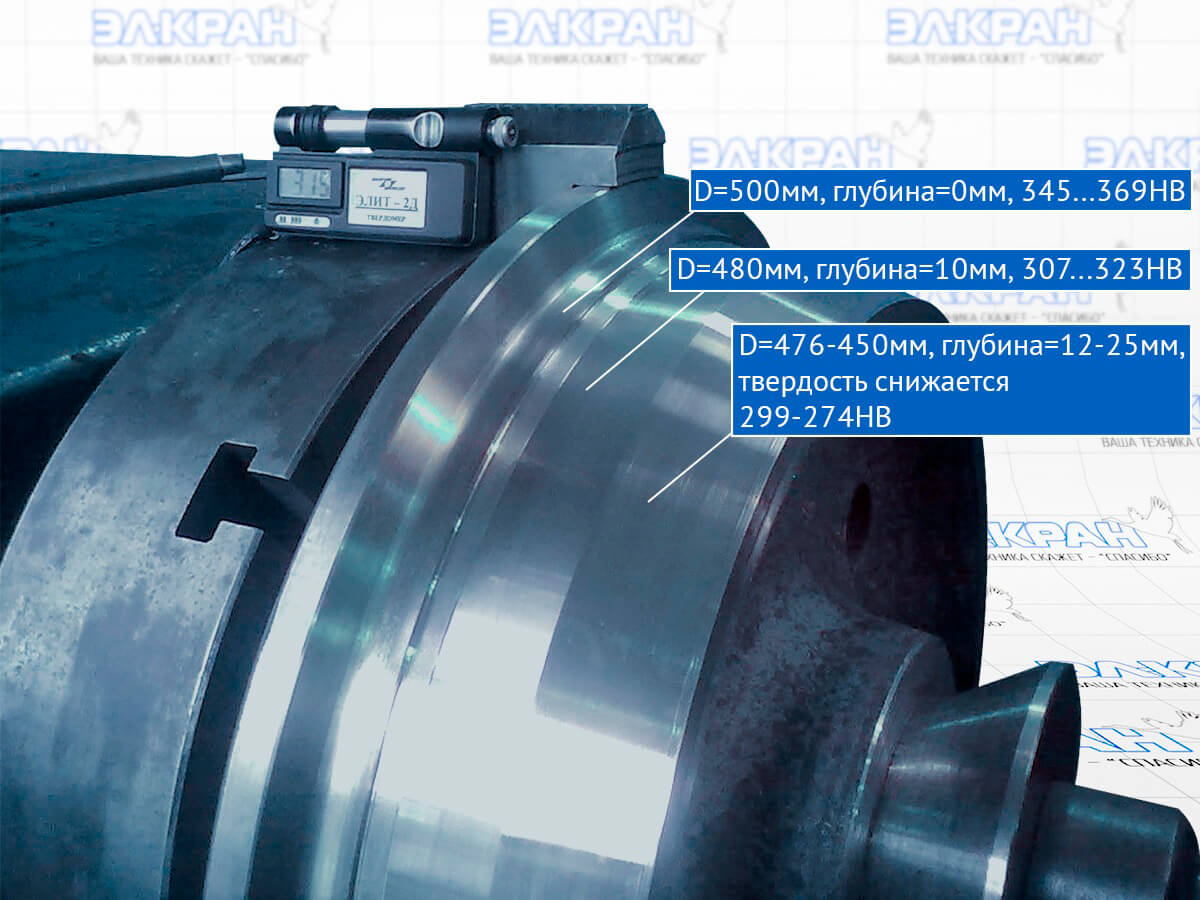
Фото 2. Методы контроля закаленного слоя крановых колес
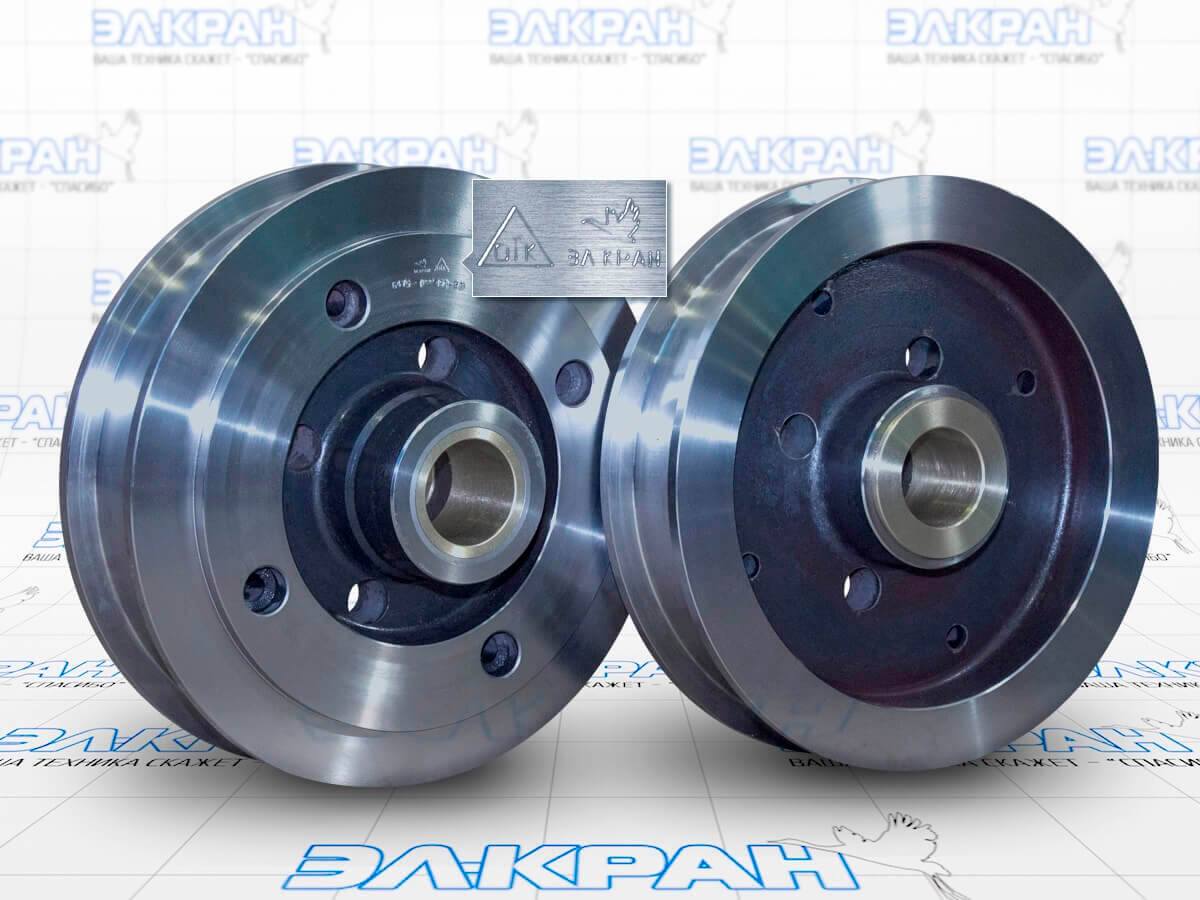
Фото 3. Ходовые колеса грейферного крана с бронзовыми втулками
3. Не менее важное значение мы уделяем механической обработке. Любые токарные работы на предприятии ООО «Эл-Кран» выполняются только с применением высокоточного инструмента Hoffman Group. Абсолютно все колёса нашего производства проходят этап дополнительной чистовой токарной обработки, причём требования к классу шероховатости обрабатываемых поверхностей для нашей продукции мы по умолчанию устанавливаем существенно выше, чем регламентирует ГОСТ 28648-90. Благодаря использованию высококачественного инструмента, нам удаётся получить практически «зеркальную» рабочую поверхность колеса, что впоследствии напрямую влияет на основной вид износа – износ от трения скольжения, а, следовательно, уменьшает интенсивность истирания рабочих поверхностей колеса. Таким образом, мы добиваемся существенного повышения долговечности колёс крановых;
4. Изучение механизмов износа колёс ходовых, мер по предупреждению износа и увеличению сроков службы, собственный опыт, различные мероприятия по совершенствованию технологии изготовления и опыт заказчиков по эксплуатации нашей продукции – всё это вкупе позволило ООО «Эл-Кран» стать бесспорным лидером по изготовлению подобной продукции на сегодняшний день. Можем привести бесчисленное количество очевидных аргументов в пользу этого утверждения, но самый простой, веский и легко проверяемый из них – это отзывы наших заказчиков. Ни один поставщик аналогичной продукции не имеет подобного «послужного списка».
Актуальность проблемы:
Мостовые краны являются наиболее массовыми средствами механизации погрузо-разгрузочных работ на производстве. Ходовые колёса относятся к числу наименее долговечных их элементов. Если металлоконструкции кранов могут эксплуатироваться в течение 20-50 лет, то средний срок службы ходовых колёс составляет несколько лет, а в отдельных случаях при интенсивной эксплуатации, этот параметр может снижаться до нескольких месяцев. Расходы, связанные с заменой колёс, в большинстве случаев являются определяющими при ремонте мостовых кранов.
(Ю.К. Ионов «Механизм изнашивания ходовых колёс мостовых кранов», Днепропетровск, 1953 г.; В.А. Цыбульский «Оптимизация свойств материалов ходовых колёс мостовых кранов с целью повышения их долговечности», Харьков, 1996 г.)
Вопрос по износу ходовых колёс, несмотря на его важность, в настоящее время закрыт не полностью. Исчерпывающих систематизированных данных о механизме износа ходовых колёс не достаточно. Поэтому гарантированных однозначных решений этого вопроса тоже нет. Многофакторность условий, влияющих на явление износа колёс, не достаточная полнота данных о механизме этого процесса, а так же отсутствие полномасштабных лабораторных испытаний на изнашивание сталей, применяемых для изготовления ходовых колёс, привели к условному решению проблемы на уровне отдельных авторских работ. Некоторые из них были впоследствии воплощены в различного рода обязательные государственные отраслевые стандарты, например ГОСТ 28648-90. Другими словами, на данный момент существуют понимание и государственные требования, регламентирующие необходимый минимум для изготовления ходовых колёс. Соблюдение этого минимума можно сравнить с оценкой «удовлетворительно» в зачётной книжке студента… Задача любого уважающего себя специалиста - стремиться и получать результат «на отлично»!
Основная идея ООО «Эл-Кран» в области инженерных изысканий по этому вопросу заключается в принципе «Сохранить и преумножить»: мы кропотливо изучаем историю освещения этого вопроса в отечественном и импортном машиностроении, собираем данные и опыт по эксплуатации изготовленных на нашем предприятии ходовых колёс. Систематизируем и анализируем полученную информацию. Благодаря накапливаемому опыту, беспрерывно совершенствуем технологию механической обработки ходовых колёс, процесс проведения термической обработки, модернизируем и развиваем производственную базу нашего предприятия.
Методическая база вопроса:
Первое известное системное исследование проблемы долговечности ходовых колёс мостовых кранов было предпринято в 50-х годах XX века на базе Днепропетровского металлургического завода им. Петровского. В результате 16 месяцев практических наблюдений было установлено:
- факторами внешнего воздействия, влияющими на износ ходовых колёс, можно считать:
а) конструктивные особенности крановых мостов и ходовых частей кранов,
б) конструктивные особенности ходовых колёс,
в) правильность монтажа и точность изготовления ходовых колёс,
г) условия эксплуатации; - основной процесс износа ходовых колёс происходит в зоне соприкосновения колеса с рельсом;
- основными видами износа рабочих частей обода ходовых колёс являются следующие:
а) износ реборд ходовых колёс,
б) образование проката на поверхности качения,
в) возникновение продольных трещин на поверхности качения и связанное с ними выкрашивание металла с этой поверхности,
г) образование вмятин на рабочей поверхности ходовых колёс; - наиболее частым видом износа ходовых колёс мостового крана является износ по ребордам;
- ходовые колёса, изготовленные из кованной и/или штампованной заготовки, как ведущие, так и ведомые изнашиваются равномерно по всей окружности и по величине износа почти не отличаются друг от друга;
- ходовые колёса, изготовленные из литой заготовки склонны к неравномерному износу, в процессе эксплуатации зачастую обнаруживают внутренние структурные дефекты, приводящие к появлению трещин и сколов на поверхности качения и ребордах;
- износ ходовых колёс тем меньше, чем строже соблюдён требуемый диапазон твёрдости рабочей поверхности, микроструктура закалённого слоя, плавный переход закаленного слоя к незакаленному.
Основные выводы, которые были сделаны в процессе исследования, следующие:
1. Результаты наблюдений за износом ходовых колёс в эксплуатационных условиях, сопоставления гипсовых отпечатков, снятых с рабочих частей ободов в различные периоды эксплуатации колес, а также результаты лабораторных исследований изношенных колёс и продуктов их износа, позволяют сделать вывод, что основной причиной износа подавляющего большинства ходовых колёс является истирание, сопровождающееся пластическими деформациями поверхностных слоёв рабочих частей ободов ходовых колёс;
2. Характер перемещения ходовых колёс по подкрановым рельсам и направление деформаций в поверхностных слоях ободов ходовых дают основание считать основным видом износа – износ от трения скольжения, возникающего при поперечных и продольных проскальзываниях колёс. При этом более существенную роль играет поперечное проскальзывание ходовых колёс;
3. Ввиду того, что износ реборд и поверхностей качения ходовых колёс происходит в результате трения скольжения, целесообразно наряду с расчётом ходовых колёс по формуле Герца-Беляева производить дополнительный расчёт на истирание. Особенно важно для практики производить расчёт реборд ходовых колёс на истирание, так как износ реборд является наиболее частым видом износа. Для вывода такой формулы необходимо провести широкие испытания на изнашивание сталей, употребляемых для изготовления ходовых колёс, на специальной машине трения, воспроизводящей работу двухребордных колёс на подкрановом рельсе;
4. Исходя из металлографических исследований ходовых колёс, находившихся различное время в эксплуатации и имеющих различные виды и степень износа, можно сделать вывод о том, что для изготовления колёс мостовых кранов должны употребляться стали, имеющие химический состав, близкий к эвтектоидному, имеющие равновесную кристаллическую решётку. Микроструктура рабочих поверхностей колёс должна представлять собой мелкопластинчатый перлит, в идеале – сорбит (мелкодисперсная разновидность перлита);
5. Повышение твёрдости рабочей части обода посредством термической обработки (закалки) целесообразно производить до 300…360 НВ для поверхности качения ходовых колёс и до 350…400 НВ для реборд. Дальнейшее увеличение твёрдости допустимо только в случае повышения твёрдости головок подкрановых рельсов.
(Ю.К. Ионов «Механизм изнашивания ходовых колёс мостовых кранов», Днепропетровск, 1953 г.)
Выводы более поздних исследований развивают и уточняют результаты, полученные под руководством Ионова, а именно:
1. При ходовых колёсах с коническим ободом мостовых кранов с центральным механизмом передвижения забегание одной стороны крана относительно другой вызывает качение отстающего ходового колеса по большому диаметру и автоматическое уменьшение перекоса. Ожидалось, что такое решение существенно увеличит срок службы конических колёс по сравнению с цилиндрическими. К сожалению, вследствие высоких контактных напряжений, коническая поверхность быстро изнашивается, и в работу включаются реборды аналогично цилиндрическим колёсам. Т.о., практика показала, что колёса с коническим ободом имеют меньший эксплуатационный ресурс чем колёса с цилиндрическим ободом;
2. Принято считать, что основной причиной повышенного износа колёс кранов с раздельным механизмом передвижения является непараллельность осей подкрановых рельсов. К сожалению, даже идеальная установка рельсов не устранит перекос моста крана во время движения. К этому приводит несовпадение характеристик приводных двигателей и преимущественно нецентральное положение транспортируемого груза. Смещение груза от центра крана увеличивает нагрузку на соответствующий двигатель, и он снижает скорость своего вращения. Вращение левого и правого двигателей с разными угловыми скоростями ведет к забеганию одной стороны крана относительно другой. При движении крана с перекосом, реборды колёс ходовых колёс постоянно трутся о рельсы. Это ведет к интенсивному износу реборды и боковых поверхностей рельсов. Т.о., правильное упрочнение рабочей части колеса, включая реборды, крайне важно.
(Щеглов О.М., Сагиров Ю.Г., Суглобов Р.В. «К вопросу о повышении долговочности ходовых колёс мостовых кранов», Мариуполь, 2010 г.);
3. Выполненные исследования показали, что стальные заготовки по ГОСТ 14959-79 (Прокат из рессорно-пружинной углеродистой и легированной стали), ГОСТ 8479-70 (Поковки из конструкционной углеродистой и легированной стали), ТУ 14-1-2118-98 (Прокат горячекатаный сортовой в профилях размером 250 мм и более из конструкционной углеродистой и легированной стали) являются предпочтительным материалом для изготовления ходовых колёс мостовых кранов. Такой материал обладает стабильными механическими характеристиками и износостойкостью, позволяет получить стабильный и прогнозируемый результат при проведении термической обработки. Другими словами, проведённые испытания показали, что колёса, изготовленные из стальной поковки, или штамповки, или горячекатаного круга из марок стали 45, 40Х, 65Г по своим эксплуатационным характеристикам, износостойкости и долговечности в разы превосходят колёса, изготовленные из литых заготовок. Т.к., кованные и/или штампованные заготовки обеспечивают более высокую надёжность конструкции колеса (меньшую склонность к образованию трещин и внезапному разрушению в процессе производства и эксплуатации), а так же более чем в два раза менее интенсивно изнашивают материал подкранового пути (рельса);
4. Качество термической обработки колёс во время закаливания оценивается степенью стабильности их механических свойств, получаемых в результате. Оценка нормируемого показателя твёрдости должна находиться под постоянным контролем, поскольку неконтролируемый процесс науглероживания и обезуглероживания стали является вредным, так как приводит к большому разбросу механических свойств на разных уровнях поверхности колеса, что является одной из серьёзных причин неравномерного изнашивания ходовых колёс;
5. В качестве мероприятий, улучшающих качество закалки крановых колёс, можно рекомендовать следующие: исключение непосредственного контакта кранового колеса с пламенем газовой горелки в нагревательной печи; предпочтительно использование электрических печей шахтного типа; специальный припуск на поверхности кранового колеса под термическую обработку, который необходимо удалять после закалки, величину припуска целесообразно брать не менее 1 мм.
(В.А. Цыбульский, А.А. Концевич, Э.А. Тимченко, «Повышение долговечности колёс мостовых кранов при техническом обслуживании и ремонте», Харьков, 2013 г.)